PRINCE
PRocess INnovation Center – Wettbewerbsfähig mit Industrie 4.0 und Künstlicher Intelligenz (KI)
Projektdauer
20.05.2020 - 31.07.2025
Förderkennzeichnung
H.5-H3361.LA/3/4
Gefördert durch
Bayerisches Staatsministerium für Wissenschaft und Kunst
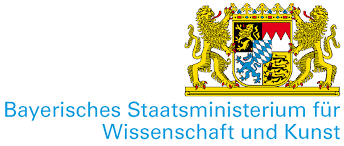
SDG
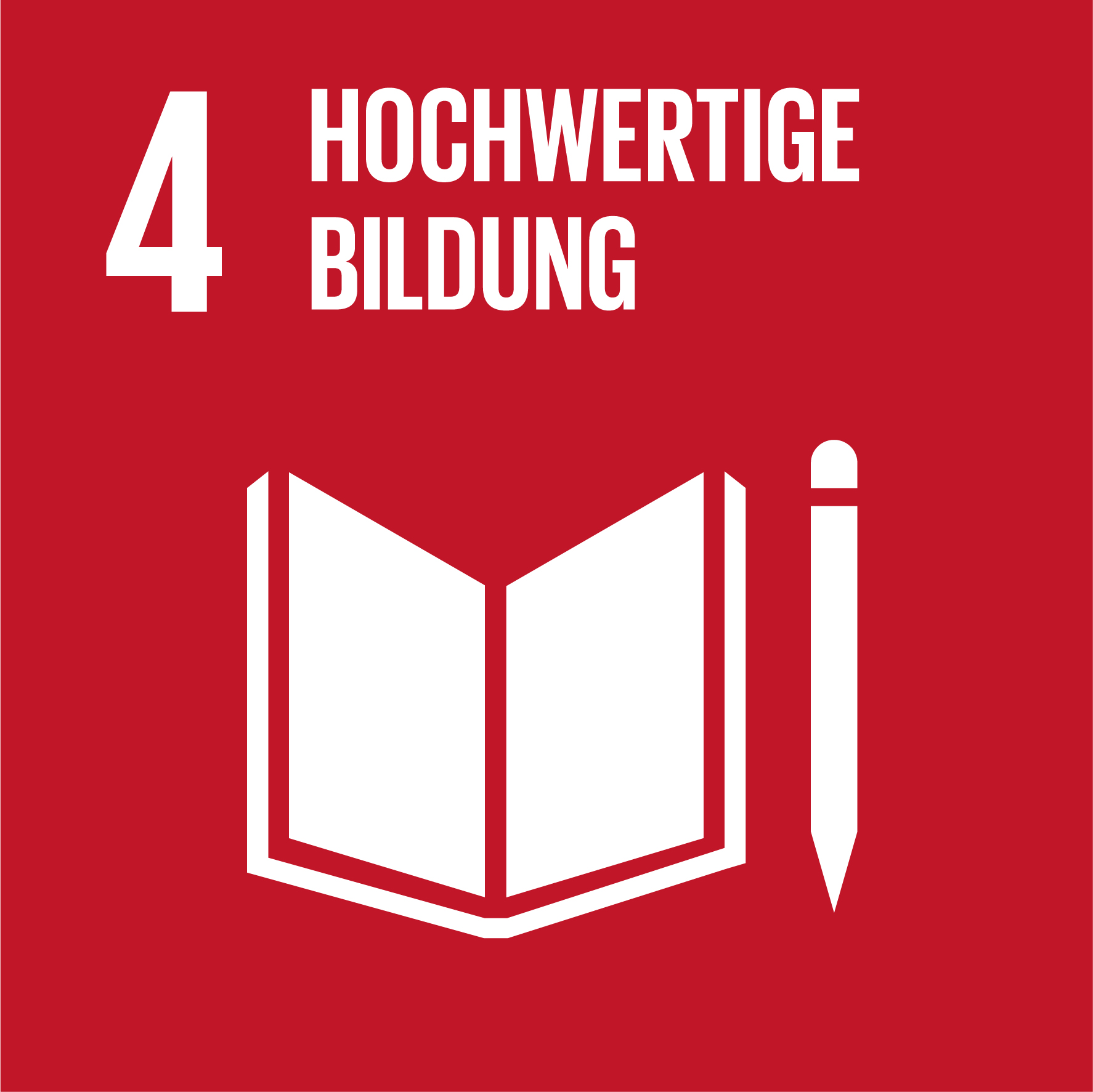
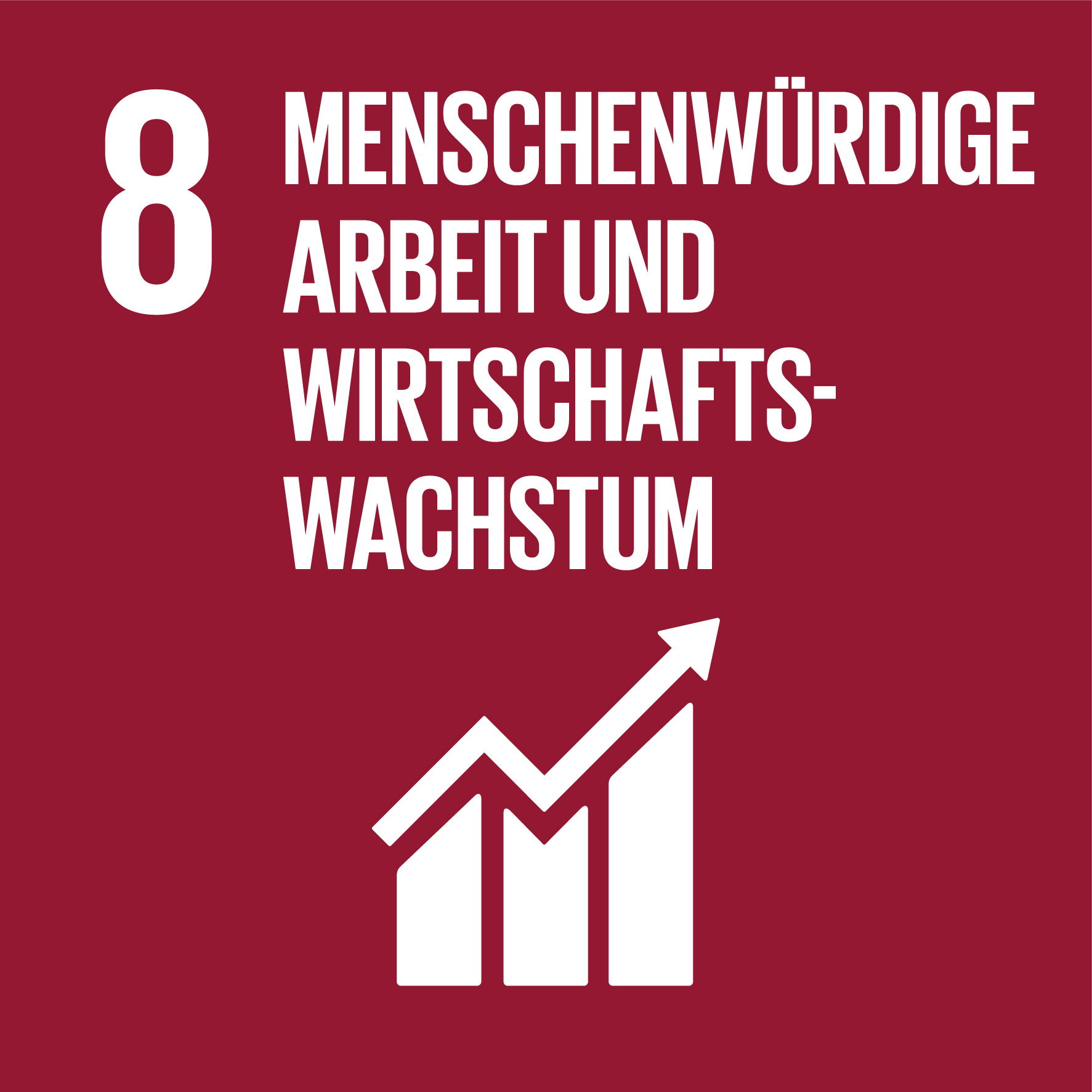
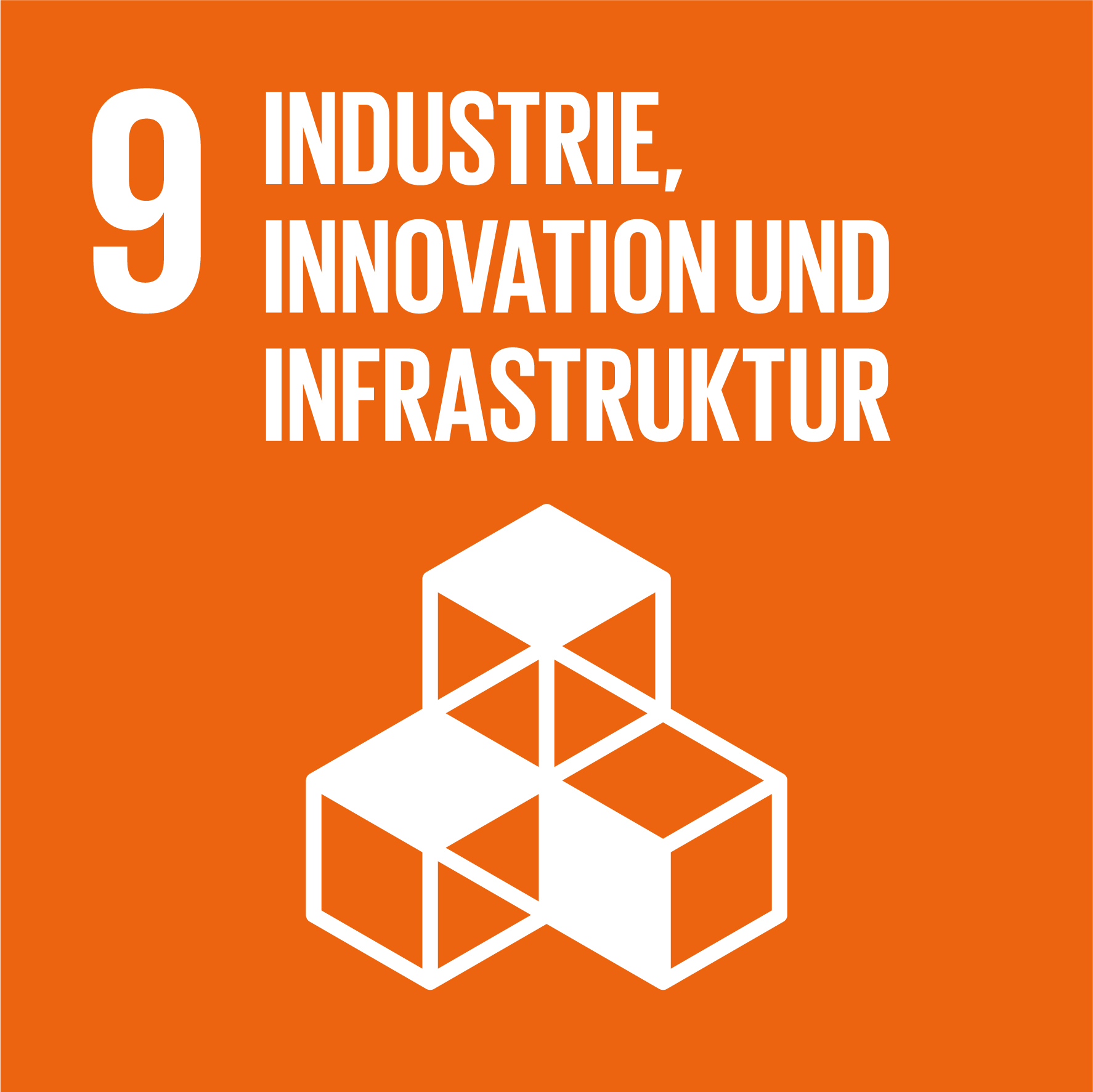
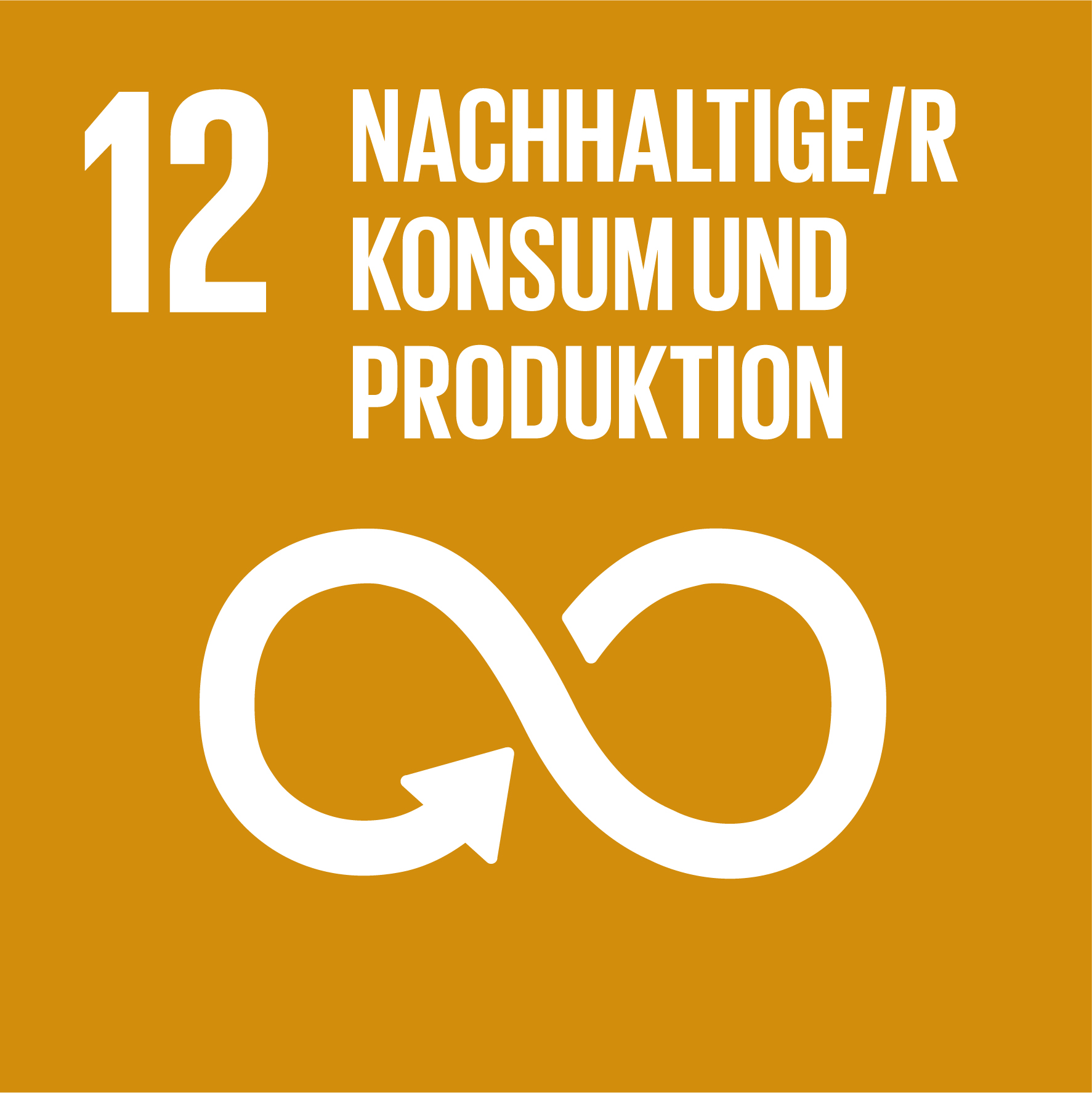
Beteiligte Personen
Gesamtprojektleitung :
Prof. Dr. Markus Schneider
Projektleitung Hochschule Landshut:
Prof. Dr. Sebastian Meissner
Prof. Dr. Carsten Roeh
Wissenschaftliche Mitarbeitende:
Tobias Ettengruber
Corinna Huber
Marion Lemke
Lisa Schuler
PRINCE
PRocess INnovation Center – Wettbewerbsfähig mit Industrie 4.0 und Künstlicher Intelligenz (KI)
PRocess INnovation CEnter PR|IN|CE
Dauerhafte Wettbewerbsfähigkeit setzt ständig steigende Produktivität voraus (Wirtschaftsnobelpreisträger Paul Krugman). Das bedeutet, dass Güter und Dienstleistungen mit weniger Ressourcenverbrauch erbracht werden müssen. Dies erreicht man einerseits durch kontinuierliche Prozessverbesserungen und andererseits durch große Produktivitätssprünge, indem man Prozesse radikal erneuert. Bisher spielt sich das Thema Innovation jedoch fast nur auf der Produktebene ab.
Das PR|IN|CE-Projekt zielt darauf ab, die Wettbewerbsfähigkeit des produzierenden Gewerbes in Deutschland durch Prozessinnovationen in Produktion und Logistik zu steigern. Die beteiligten Wissenschaftler*innen bauen die bestehenden Strukturen des Technologiezentrums PULS zum „PRocess INnovation CEnter – PR|IN|CE“ aus, entwickeln radikale Ideen zur Neugestaltung unternehmensspezifischer Produktions- und Logistikprozesse auf wissenschaftlicher Basis und testen unmittelbar die umsetzungsreifen Prozessinnovationen.
Beteiligte Professoren:
Markus Schneider, Sebastian Meißner, Carsten Röh
Wissenschaftliche Mitarbeiter*innen:
Tobias Ettengruber, Marion Lemke, Lisa Schuler
Projektdaten:
- Projektlaufzeit: 01.08.2020 bis 31.07.2025
- Gefördert durch das Bayerische Staatsministerium für Wissenschaft und Kunst
- Fördersumme Gesamtprojekt PR|IN|CE: 2,6 Millionen Euro
Digitaler Zwilling
Ist die Materialreichweite groß genug? Wie sieht die Ressourcenauslastung aus, müssen Kapazitäten angepasst werden? Welche Auswirkungen hat die verspätete Lieferung?
Mit diesen Fragen sehen sich viele Unternehmen konfrontiert. In der Praxis erhalten sie oftmals erst dann Antwort auf diese Fragen, wenn bereits eine Störung im Materialfluss aufgetreten ist; es also meistens bereits zu spät ist. Um diesen Engpasssituationen vorzubeugen, bauen Unternehmen häufig einen hohen Sicherheitsbestand auf. Als Folge wird sehr viel Kapital gebunden und die Komplexität der Steuerung steigt. Eine Technologie, die diese Probleme lösen kann ist der Digitale Prozesszwilling. Digitale Prozesszwillinge ermöglichen eine rechtzeitige und präventive Reaktion auf die volatilen Umfeldeinflüsse in der Produktionslogistik. Sie sind funktionale, dynamische Abbilder von Systemen (Prozesse, Anlagen, …), welche mithilfe von Modellen, Algorithmen und Services, Prozesse identifizieren, Schwachstellen aufzeigen und mittels Vorhersagen präventiv optimieren können. Jedoch werden Digitale Prozesszwillinge bisher kaum in der Logistik eingesetzt, da das Knowhow fehlt. Aufgabe des Teilprojektes Digitaler Zwilling ist es Unternehmen bei der Planung und Einführung von Digitalen Prozesszwillingen, insbesondere im Bereich der Produktionslogistik, zu unterstützen. Dazu werden Vorgehensweisen und Methoden praxisnah erforscht. Teile davon sollen eine spezifische Prozessanalyse-Methodik hinsichtlich Digitaler Zwillinge, eine geeignete Architektur, sowie strukturierte methodenbasierte Vorgehensweisen zur Planung darstellen. Ebenso werden die Zusammenhänge zwischen Funktionen und notwendigen Software/ Hardware Elementen inkl. deren Relationen zueinander erforscht. Parallel zur Gewährleistung der Praxisnähe, wird ein Demonstrator am Technologiezentrum Produktions- und Logistiksysteme geplant und umgesetzt. Dabei werden Regale zu intelligenten Materialflusselementen aufgerüstet, welche in Echtzeit Statusinformationen senden. Eine Simulationsmodell wird erstellt und an aktuelle Prozessdaten angebunden, um Prognosen zu ermöglichen. Ebenso sollen Alternativszenarien simuliert und bewertet werden, sodass auf die schwankenden Einflussgrößen in der Produktionslogistik präventiv und rechtzeitig bestmöglich reagiert werden kann. Ziel ist es dabei, einerseits die erforschten Methoden anzuwenden und andererseits ein besseres Verständnis für Digitale Zwillinge zu schaffen. Dies soll die Brücke zwischen Wissenschaft und Praxis bilden, um Digitale Zwillinge als unterstützendes Werkzeug in den Unternehmen zu etablieren.
Ansprechpersonen:
M.Eng. Corinna Huber
Projektverantwortliche
Prof. Dr.-Ing. Dipl.-Wirtsch.Ing. Sebastian Meißner
Projektleiter
Vernetzung & Automatisierung
Motivation
Durch die kontinuierlichen Weiterentwicklungen sowie neue Technologien im Bereich der Industrie 4.0 gibt es viele Möglichkeiten, Prozesse zu automatisieren und die eingesetzten Systeme miteinander zu vernetzen.
§ HHerausforderung 1: Welche Prozesse sollen (zuerst) in der Produktion und Logistik automatisiert werden?
§ HHerausforderung 2: Wie sollen die einzelnen Systeme zu einem Gesamtsystem vernetzt werden?
§ HHerausforderung 3: Welche Technologien sollen dabei eingesetzt werden?
Im Rahmen der Weiterentwicklung der Musterfabrik werden die einzelnen Fragestellungen analysiert, implementiert und evaluiert.
Projektziele
- Automatisierung in der Produktion und Logistik – Schwerpunkt Prozessautomatisierung in der Intralogistik
- Einsatz von verschiedenen sinnvollen und innovativen Technologien für Produktion und Logistik sowie Integration dieser Systeme in der OT-/IT-Landschaft
- Anwendung von einheitlichen Kommunikationsschnittstellen zwischen Systemen und damit Auswahl der effizienten Lösungen aus den auf den Markt verfügbaren Lösungen.
- Erarbeitung einer einheitlichen Beschreibung der Systeme und des Informationsflusses mit einer Referenzarchitektur geeignet für KMU
Ansprechpersonen:
M.Sc. Lisa Schuler
Projektverantwortliche
Prof. Dr. rer. pol. Markus Schneider
Projektleiter
Maschinelles Lernen in der Produktionsplanung und -steuerung
Das Handlungsumfeld der Produktionsplanung und -steuerung ist vermehrt geprägt von Komplexität, Unsicherheit und Dynamik, wodurch die produktionslogistische Zielerreichung für Unternehmen erschwert wird. Menschliche Wahrnehmung und Erfahrung alleine reicht oftmals nicht mehr aus. In der Praxis werden daher vermehrt regelbasierte Assistenzsysteme zur Unterstützung der Mitarbeiter eingesetzt. Diese regelbasierten Assistenzsysteme verursachen einen hohen Aufwand für Wissensakquisition und -aktualisierung, was für Unternehmen im vorliegenden komplexen und turbulenten Umfeld immer häufiger ein Problem darstellt. Eine mögliche Lösung hierfür ist der Einsatz von künstlicher Intelligenz bzw., von maschinellem Lernen (M). ML-Verfahren sind datengetriebene Ansätze, die komplexe, nicht lineare Muster in Daten erkennen können und dadurch in der Lage sind, Wissen aus bestehenden Daten zu generieren. Prozesse der Produktionsplanung und -steuerung können somit durch die Verwendung von ML mit der Fähigkeit des selbständigen Lernens ausgestattet werden.
Durch den zunehmenden Einsatz von cyberphysischen Systemen ist eine deutlich größere Menge an Informationen nahezu in Echtzeit verfügbar, welche für Planungs- und Steuerungsaufgaben herangezogen werden kann. Jedoch haben konventionelle Methoden der Produktionsplanung und -steuerung Schwierigkeiten, diese gesteigerte Informationsmenge zu verarbeiten und entscheidungsrelevante Aspekte herauszufiltern. Daher soll im Rahmen dieses Projektes erforscht werden, inwieweit die Produktionsplanung und -steuerung durch Verfahren des maschinellen Lernens verbessert werden kann und welche Barrieren eine Implementierung gegenwärtig erschweren.
Projektschwerpunkte
- Erforschung der gegenwärtigen Nutzung von ML im Bereich der Produktionsplanung und Steuerung in Wissenschaft und Praxis
- Untersuchung der PPS-Aufgaben im Hinblick auf die Eignung eines ML Einsatzes
- Erforschung von Implementierungshürden in Bezug auf ML-Anwendungen im PPS-Umfeld
- Generierung von Applikationswissen und Ableitung von Handlungsempfehlungen für den situativen Einsatz von ML-gestützten Assistenzsystemen in der Produktionsplanung und -steuerung
Ansprechpersonen:
M.Eng. Konstantin Büttner
Projektverantwortlicher
Prof. Dr. rer. pol. Markus Schneider
Projektleiter
Innovativer Materiallfluss & Process Prototyping
Das Teilprojekt „Innovativer Materialfluss & Process Prototyping“ des Forschungsprojekts PR|IN|CE hat sich zum Ziel gesetzt, radikale Prozessideen auf dem Gebiet der Produktions- und Logistiksysteme innerhalb weniger Tage in der Lern- und Musterfabrik umzusetzen. Um dieses Ziel zu erreichen wurde das Konzept des modularen und skalierbaren Process Prototyping Baukastens entwickelt. In Abbildung 1 sind die Kernelemente dieses flexiblen Systems dargestellt.
Abbildung 1: Struktur des Process Prototyping
Der Aufbau ganzer Prozessabläufe innerhalb weniger Tage kann nur durch eine einfache logische Vernetzung der Systeme erfolgen. Basis hierfür bildet die Serviceorientierte Datenarchitektur des Process Prototyping Baukastens. Mittels Schnittstellenprotokolle wie MQTT oder OPC-UA können Daten orchestriert und serviceorientiert bereitgestellt werden. Mit dem Entwicklungswerkzeug Node-RED werden diese Daten der einzelnen Prozessschritte zu einem logischen Ablauf verknüpft.
Die Hardware Basis des Process Prototyping Baukastens bildet die Technik der Lern- und Musterfabrik des TZ PULS. Hierzu werden die vorhandenen Technologien stetig weiterentwickelt und in das Process Prototyping Umfeld eingebunden. Ein Beispiel ist das im Abbildung 2 dargestellte Fahrerlosentransportfahrzeug - Jungheinrich EKS215a.
Abbildung 2: FTF im Einsatz in der Musterfabrik
Ergänzend zu den Systemen in der Lern- und Musterfabrik werden sogenannte „Prototyping 4.0 Module“ eingesetzt. Diese Module stellen spezifische Funktionen in den Bereichen Kommunikation, Sensorik, Kameratechnik (Vision), Wireless Datenübertragung und Kollaborative Greiftechnik dar.
Abbildung 3: Prototyping 4.0 Modul – „Vision“
Derzeit im Aufbau befindet sich das Process Automation Center (PAC). Diese integriere Roboterzelle soll neben automatisierten, logistischen Prozessen auch das Rapid Prototyping von Bauteilen, Bauteilaufnahmen oder Befestigungen für Sensoren aus Kunststoff oder Holz abbilden können. Mittels dieser „Eigenfertigung“ können die Technologien der Musterfabrik kurzfristig und kostengünstig an die verschiedenen Gegebenheiten und Produkte bzw. Prozesse der Partnerunternehmen angepasst werden.
Abbildung 4: Konzept Process Automation Center (PAC)
Eine weitere wichtige Komponente des Baukastens ist die Process Prototyping Werkstatt. Hier werden mechanische aber auch elektrische Anpassungen und Ergänzung für das Process Prototyping in der Musterfabrik durchgeführt.
Abbildung 5: Process Prototyping Werkstatt
Ansprechpersonen:
M.Eng. Tobias Ettengruber
Projektverantwortlicher
Prof. Dr. rer. pol. Markus Schneider
Projektleiter
Lieferantenpotentiale
Lieferanten – verstanden als Träger der Unternehmens-externen Wertschöpfung – sind zentrale Impulsgeber für Innovationen. Während Kunden primär Impulse für Produktinnovationen liefern, geben Lieferanten Innovationsanstöße für Prozessinnovationen (Antonelli & Fassio, 2016).
Zudem ist kaum ein Unternehmen in der Lage, eine (logistische) Prozessinnovation vollumfänglich intern zu entwickeln und umzusetzen, sondern ist auf Externe angewiesen – zum Beispiel für das Programmieren von IT-Lösungen. Entsprechend sind zahlreiche Lieferanten in Prozessinnovations-Projekte involviert und können als aktive Partner sowohl in der Ideenentwicklung als auch in der Umsetzung beteiligt sein.
Lieferanten können:
- Expertise oder Anlagen liefern,
- als Impuls- und Ideengeber fungieren und/oder
- kooperativ in der Realisierung einer Prozessinnovation beteiligt sein.
Wie Unternehmen diese „Lieferantenpotentiale“ bestmöglich erkennen und nutzen können, ist die zentrale Fragestellung des Teilprojekts „Lieferantenpotentiale“ im Projekt PRINCE. Konkret wird erforscht, wie die Schnittstelle zwischen Unternehmen und dessen Lieferanten – verstanden als die Beschaffungsfunktion – in Projekten zu logistischen Prozessinnovationen vorgehen sollte. Die Forschungsergebnisse werden in Zusammenarbeit mit Unternehmen und mit den Schwerpunkten der anderen Teilprojekten praxisnah erprobt und in einem „Werkzeugkasten der Beschaffung für logistische Prozessinnovationen“ gebündelt und dokumentiert, und so verfügbar gemacht.
Möchten Sie sich beteiligen oder fachlich austauschen? Dann wenden Sie sich gerne an uns!
Ansprechpersonen:
Dipl.-Math. oec. Marion Lemke
Projektverantwortliche
Prof. Dr. rer. pol. Carsten Röh
Projektleiter